The Power of Polyaspartic
Floor Coating
A quick cure for durable floors
FAST
EFFICIENT
FLEXIBLE
Introducing the
next generation
of polyaspartic
floor coatings
A swift and seamless commercial floor solution
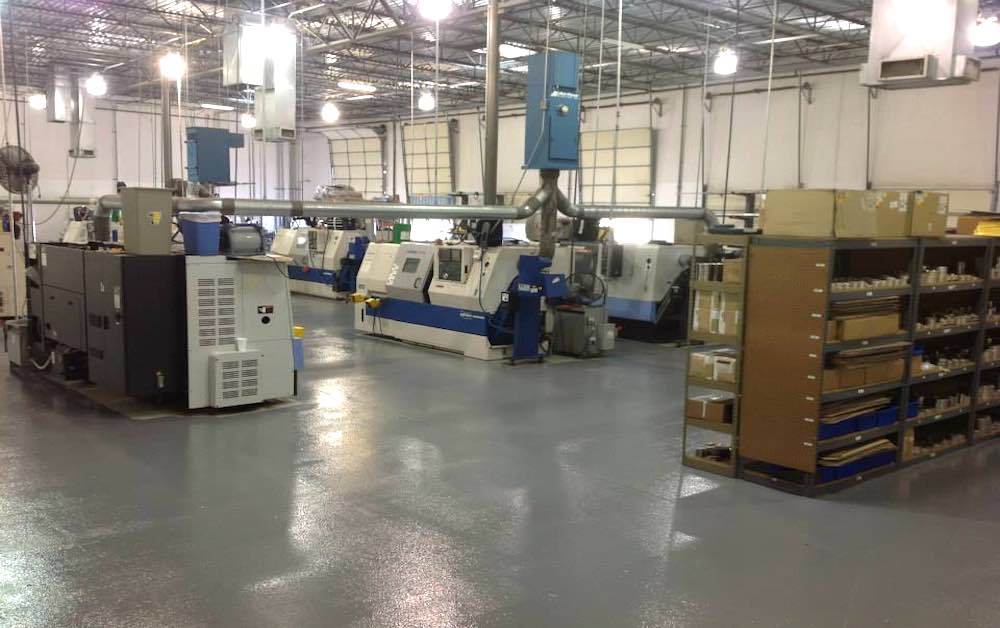
Are you tired of constantly dealing with the hassle of your commercial floors?
Do you spend too much time and money repairing chipped concrete, patching cracks, and trying to maintain a clean, professional look?
Our innovative two-part polyaspartic system, composed of resin and catalyst, is the ultimate quick cure for tired floors.
We formulate our polyaspartic coatings to deliver unbeatable speed and efficiency, ensuring your commercial floors are ready for use in record time.
But what’s more impressive is the quality and durability polyaspartic provides.
Imagine having a beautiful, shiny, and professional-looking floor that requires minimal maintenance and provides maximum longevity.
Whether you want to make a lasting impression on customers or create a safer and more ergonomic workspace for employees, our polyaspartic floor coating will help take your business to the next level.
View the transformations these businesses experienced with
polyaspartic floor coatings
Benefits of Polyaspartic Floor Coatings
Refinishing commercial floors can be time-consuming and costly, but polyaspartic coatings provide a practical alternative.
With rapid curing times, some formulations curing in as little as five minutes, polyaspartic coatings offer unparalleled efficiency.
Polyaspartic coatings also offer high abrasion resistance—higher than epoxy or urethane—and the ability to resist most stains and chemicals, ensuring longevity and durability.
Investing in polyaspartic floor coatings is a smart choice for businesses seeking to improve their space while reducing the need for frequent refinishing.
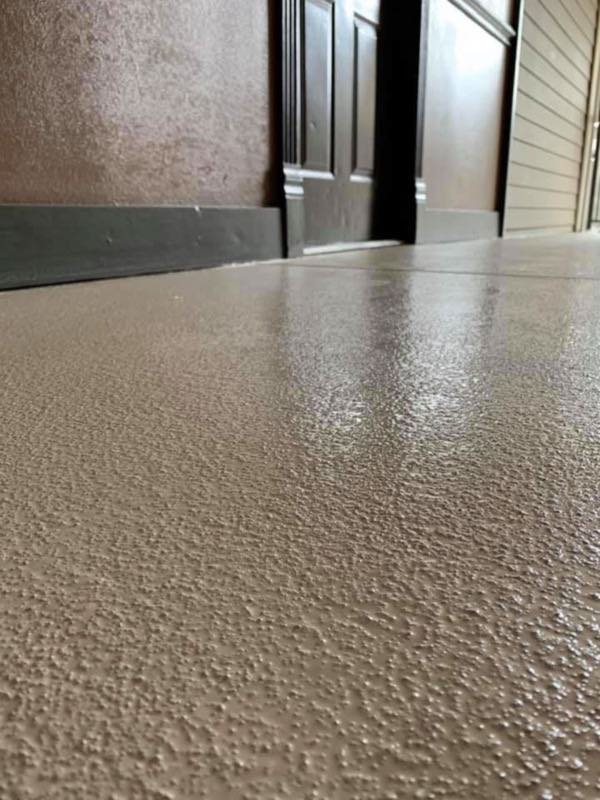
Polyaspartic Floor Coating FAQs
Is polyaspartic coating better than epoxy?
Polyaspartic and epoxy coatings are both popular options for concrete floor coatings, but the better choice depends on the specific needs and requirements of the project.
Additionally, polyaspartic coatings are also known for their fast curing time, allowing quicker installation and less downtime. They also have excellent UV resistance, which makes them ideal for outdoor applications.
Polyaspartic coatings are highly durable and chemical resistant, making them a good choice for industrial and commercial settings.
Epoxy coatings have been popular for concrete floors for many years. Epoxy coatings are known for their high durability, abrasion resistance, and ability to bond well with concrete surfaces. They are also resistant to chemicals and provide a smooth, glossy finish.
In terms of cost, polyaspartic coatings are typically more expensive than epoxy coatings, but their fast curing time can offset this cost by reducing labor and downtime.
Ultimately, the choice between polyaspartic and epoxy coatings depends on the project’s specific needs. Factors such as curing time, durability, chemical resistance, and cost should all be considered when selecting a coating.
Is polyaspartic floor coating worth it?
Polyaspartic floor coating can be worth it for many applications, depending on the specific needs and requirements of the project.
Here are some benefits of polyaspartic floor coatings to consider:
- Fast curing time: Polyaspartic coatings cure quickly, allowing for a quicker installation and less downtime.
- Durability: Polyaspartic coatings are highly durable and resistant to abrasions, impacts, and chemicals, making them ideal for industrial and commercial settings.
- UV resistance: Polyaspartic coatings are highly resistant to UV light, making them ideal for outdoor applications.
- Glossy finish: Polyaspartic coatings can provide a glossy, smooth finish that enhances the appearance of concrete floors.
- Low maintenance: Polyaspartic coatings require minimal maintenance and are easy to clean.
However, polyaspartic floor coatings, including epoxy coatings, can be more expensive than other types.
Therefore, it is important to consider the specific needs and requirements of the project, as well as the budget, before deciding whether a polyaspartic coating is worth it.
What are the polyaspartic floor coating advantages?
Polyaspartic floor coatings offer many advantages, including:
- Rapid curing time: Polyaspartic coatings cure quickly, typically within 5 to 120 minutes, depending on the formulation.
- High humidity tolerance: Polyaspartic coatings can cure quickly even in high humidity, which can be helpful in humid environments.
- Wide temperature range: We can apply polyaspartic coatings at surface temperatures ranging from -30°F to 140°F, making them suitable for various environments.
- Low viscosity: Polyaspartic coatings have a low viscosity, which allows them to penetrate and wet concrete floors effectively.
- High film build: Polyaspartic coatings can achieve high film build, up to 18 mils in a single coat, which reduces the number of coats needed.
- Bubble-free surfaces: Polyaspartic coatings can produce bubble-free surfaces even in high humidity, enhancing the floor’s appearance.
- UV stability: Polyaspartic coatings are UV stable and do not turn yellow over time. They can also provide UV protection to underlying coatings.
- Hot tire pickup resistance: The cured coating can handle hot tire pickup at temperatures up to 350°F, making it suitable for garages and other high-traffic areas.
- Crystal-clear appearance: Polyaspartic coatings do not blush white from moisture in the concrete, maintaining a crystal-clear appearance.
- Chemical resistance: Polyaspartic coatings can resist most stains and household chemicals, making them ideal for residential and commercial settings.
- High abrasion resistance: Polyaspartic coatings offer higher abrasion resistance than epoxy or urethane coatings, making them suitable for high-traffic areas.
What are the polyaspartic floor coating disadvantages?
While polyaspartic floor coatings offer many advantages, there are also some disadvantages to consider, including:
- Cost: Polyaspartic coatings are more expensive than other types, such as epoxy coatings.
- Pot life: Polyaspartic coatings have a shorter pot life (when the coating is applied) than other coatings, so it is essential to work quickly.
- Complex application: Polyaspartic coatings can be challenging to apply, requiring specialized equipment and experienced professionals.
- Strong odor: Polyaspartic coatings can emit a strong smell during the application, which may require ventilation or respiratory protection.
- Adhesion issues: Polyaspartic coatings may have adhesion issues if the substrate is not prepared correctly, which can cause peeling or flaking.
- Slipperiness: Some polyaspartic coatings can be slippery when wet, which can be a safety hazard in specific environments.
- Limited color options: Polyaspartic coatings offer limited color options compared to other coatings.
- Not suitable for all substrates: Polyaspartic coatings are typically not ideal for use on all substrates, such as wood or metal.
It is essential to consider these disadvantages when deciding whether a polyaspartic coating is appropriate for a specific project.
What is the installation like for polyaspartic floor coatings?
The installation process for polyaspartic floor coatings typically involves the following steps, which are completed within one day:
- Surface preparation: The concrete substrate must be thoroughly cleaned and prepared to ensure proper coating adhesion. This may involve diamond grinding, shot blasting, or other methods to remove existing coatings, stains, or contaminants.
- Repairs: We must repair any cracks or other damage to the concrete surface using a suitable patching material.
- Primer application: We typically apply a primer to the surface to enhance the adhesion of the polyaspartic coating.
- Base coat application: The first layer of polyaspartic coating applies to the surface at a thickness of around 3-5 mils. We can tint or color this layer as desired.
- Optional intermediate coat application: Depending on the desired thickness of the final coating, we may apply one or more intermediate layers between the base coat and topcoat layers.
- Topcoat application: The last layer of polyaspartic coating applies to the surface at a thickness of around 3-5 mils. We can also tint or color this layer as desired.
- Curing: The curing process for the polyaspartic coating typically cures rapidly, within a matter of hours, and allows walking on it within 24 hours. However, we recommend waiting 48-72 hours before allowing heavy foot or vehicle traffic on the surface.
The installation process for polyaspartic floor coatings requires specialized equipment and experienced professionals, so hiring a qualified contractor, such as Xpedite Coatings, is essential.
How long does a polyaspartic floor last?
Polyaspartic floor coatings are known for their durability and long-lasting performance.
However, the lifespan of a polyaspartic floor coating can depend on several factors, including the quality of the coating material, the surface preparation, and the level of traffic and use the floor receives.
A polyaspartic floor coating can last up to 20 years or more when installed properly and maintained appropriately.
However, it is essential to note that the lifespan of the coating can vary based on the conditions and usage of the floor.
For example, a polyaspartic coating in a commercial or industrial setting with heavy traffic and frequent use may require regular maintenance or recoating than a coating in a residential setting with lighter traffic.
Regular cleaning and maintenance, including periodic reapplication of a topcoat to refresh the surface, can help extend the life of a polyaspartic floor coating.